Why do we have quality departments? Even posing the question feels like a minor rebellion on my part, since “Quality” is such an integral concept in the business of producing things. For “integral” we can also read “taken for granted.” Sometimes it can be good to tug at the tent poles of the status quo and see whether it collapses in a heap around us, or if we can move it somewhere more interesting.
This post isn’t just coming from a theoretical standpoint, of course. I’ve had so many run-ins with colleagues from quality that I simply have to question that whole role. Too often have they acted as alarmist messengers and chasers of other peoples' actions whilst understanding neither the problem nor the product nor the processes that they are supposed to be monitoring - that is, seemingly doing nothing about it themselves. They don’t add value, nor do they seem to save value - they transmit urgency. Unfortunately, transmitting urgency to the wrong sort of person (for example, me) is precisely the least good way of getting things resolved quickly and effectively.
So, whilst we all inherently understand the idea of producing things in ways acceptable both to customers and to our finances, do we really need quality departments, quality managers, quality engineers? I think we could be cannier about the whole thing - and ditch them totally.
The best way to do that would be to design an engineering company from scratch - alas, not something that I’ve ever done. But for me, the basic idea would be that the tasks that quality departments undertake can be distributed amongst other departments where those tasks make more sense.
The flip-flop question is this: is it better to decentralise those tasks amongst experts, or to collect them all under one roof and standardise? It may well be that the size of a company - tipping around a certain critical morass - is probably a key factor in this decision. But the prospect of ISO / TS audits should not be!
I work for a largish automotive supplier, and we have quality departments coming out of our ears: it’s the world I live in. Deleting them (distributing them) would mean for me personally that I would need to get my designs, from material selection through to defining tolerances, just right; my colleagues in production would have to design their processes to produce within the parameters of the drawings and specs I give them and that all needs to be validated and monitored.
In other words, nothing: eliminating the quality department would have no effect on my key role, nor on the role of my friends in process engineering.
However, I’m forever getting involved in quality concerns, analysing returned or quarantined parts, performing root-cause analyses. This can help me understand our product better, but rarely have I had to change a design as a result of these investigations. Enfolding one or two of our colleagues from quality into our test and development organisation would mean that those defects could been analysed as thoroughly as they are now, and lessons learned could be centralised, whilst freeing me to work on the next generation of products, which is what, I believe, I’m supposed to be doing.
Manufacturing will still need people and systems to check and to confirm that product meets requirements, both at any given instant and over time - that’s for sure; such roles will never go away, but these days we can trust our production team’s integrity to manage that by themselves rather than abdicating that responsibility to a separate department.
The role of a quality department as independent arbiter, a kind of internal auditor, remains an interesting point: can we be sure that Manufacturing, for example, will always be open and honest enough about things like tool release decisions and scrap rates when deliveries or performance indicators are on the line? Well, if we can’t be sure then it would surely be beneficial to work on the culture of the company rather than to add layers of oversight. Again, it’s a question of opportunity cost - would it be more effective for a company to pay people to police their own people, or to research and to produce things more effectively?
If we think (or click) back to my post on how Google tests software, we see that the key philosophy there is: the design of the product should include its testing and confirmation methods. So it should be the product and process design engineers designing this together, which makes sense to me.
And where would the resources come from to ensure that product and process design could cope with that additional work? From the now redundant quality department, of course.
That leaves the audit side of things. Of course, nobody wants to be involved in audits at any stage. But since audits are a fact of life in many industries, the product and process design teams need to be involved in designing the business systems that they use on a daily basis to use, store, distribute and to archive work. And they should be responsible for proving that these ways work both in theory and are used in practice.
So, eliminating quality departments, partially reassigning them to design and development, is the obvious answer to all of this - yet quality departments seem to grow and grow where I am. Am I missing something obvious that would really justify the existence of quality departments? Or can we continue to “Think Canny” in this funny old business of engineering, and “explode” quality departments out to other teams?
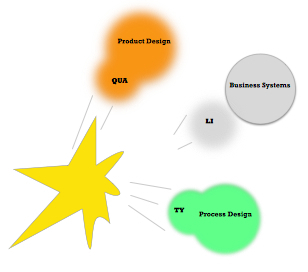