originally posted on one of my several now defunct blogs, called On Engineering, under my persona The Canny Engineer, on the 11th of May 2013
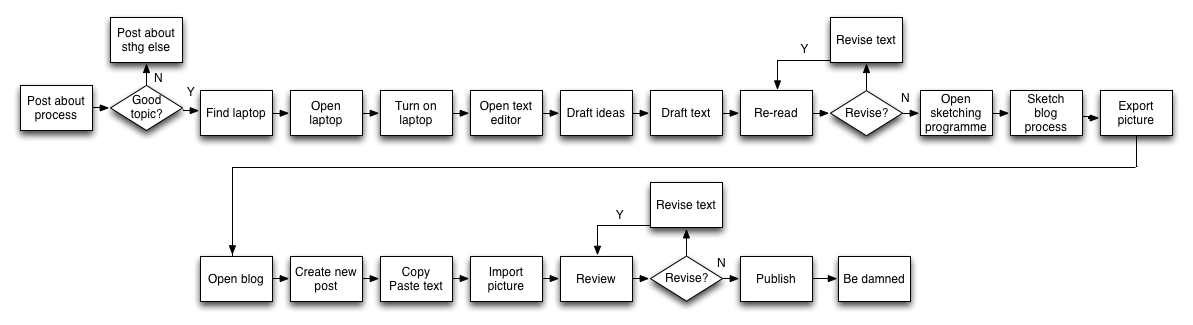
Engineers, like lawyers - hold on, I didn’t just write that, did I? Well, it’s a valid thought, so I’ll press on. Engineers, like lawyers and other animals, can be classified into distinct genera and species, depending on the path we take within our chosen vocation.
As soon as I had, whilst at school, settled on engineering as the subject I wanted to study and practice, it was clear to me that I was much more of a “boffin” type than a “hacker”. I was always uneasy about mending things, more confident about designing and working things out - so I opted for aerospace engineering. After graduation I went to Ford (emphatically not an aerospace company, despite its history and current CEO). There, I spent some time working in Manufacturing Engineering. I enjoyed the challenge, at times, but I wanted out, back to component and design engineering.
Who cares how it’s made?
Now, my job is (should be) to develop and upgrade product so that it does what it is supposed to, when it is supposed to do it under all conceivable conditions. Whilst it sounds almost blasphemous to say it in these enlightened days of openness and collaboration, I don’t necessarily care how it arrives at that point, as long as the how of its making doesn’t affect the if of its functionality, or its cost too much.
Of course, this means that I do have to care about the process, as it more often than not does affect the product in clear or in subtle ways. So I talk to our process and manufacturing engineers.
Who are, of course, also design engineers.
I suppose we have all settled into a kind of shorthand for engineering titles, as the word “design” is redundant. There are those who design and develop product, those who design and develop the process, and those who design and develop the equipment to be used in the process to make the product designed at the outset (process product design, or something like that!).
By and large, from my experience, process and manufacturing engineers are cut from a different cloth to product engineers. They can work together, but rarely does one stay in the other’s shoes for long. At the extremes, you could envisage the gnarly manufacturing engineer and the soft white-handed product engineer - of course, these types meld and merge, but the tendency is there, I feel.
And we talk.
Silos or troughs
Whether I “get to” talk to these colleagues, or “have to” depends on personalities - which, fortunately, engineers don’t have - but where I work, we are distinct groups that need to be brought together on a project by project basis; we need to jump those famous silos to work together, rather than always being together, feeding from the same trough - perhaps “collaborating freely” would be a better turn of phrase.
Our means of communication is still principally email, alas. Our offices are close enough to walk to, but all too often, simply waltzing into each others' enclosures means a disruption of some sort. We’re all busy people, who need to try and focus on some one thing at a time. Disturbances from outside, whilst of course important, mean a reshifting of focus from some other, hopefully equally important, activity. So to minimise the growling, we email or invite each other to short meetings, which is really the best method to have disparate minds alight on the one subject for a few quality minutes.
So, we have feasibility reviews, we cooperate on FMEAs (still too infrequently), we sketch, we negotiate (more often than not on tolerances), and we make, measure, test, update and approve our product.
We work together, in short.
Ideally, I should embed myself in their world so that my designs flow and interact as smoothly as possible with theirs, and their reflect the functions that the product needs to have. In small, dedicated teams, that could work, but currently it’s all about snatching time to work on one thing rather than another: even were I to share a desk with them, all we’d be doing is shouting over each others' telephone calls.
So I’ll stick to my “ivory tower” (as of course they call it), for the time being.
In praise of process
But from that tower, from behind this screen, I want to place on record my respect for my engineering cousins in process design. These are colleagues who get to play with robots, with sorting and sequencing machines, with presses and with tool designs; these are people who have a very rich and very different mind to my own.
I haven’t the faintest clue how to design and specify a press or a hopper bowl that will position and place fitting after fitting into an assembly rig so that they are all applied - firstly at all, and secondly in the correct orientation.
In some many cases, it is the process people who give one company a slender advantage over another - either through holding dimensions and quality better than anybody else, or by bringing costs down to an attractive level for everybody concerned. In the automotive world that I know, most contracts involve a year-on-year price reduction clause. This assumes that as a product achieves maturity, scrap levels are reduced, efficiency in increased and waste is minimised. These are valid assumptions to make, but the work towards achieving those goals in an economic way is principally down to the process and manufacturing engineers.
So really this post is about acknowledging the diversity within our own world of Engineering and letting it be known that I have the utmost respect for the guys and gals who, much more than Getting Things Done, Get Things Made.