originally posted on one of my several now defunct blogs, called On Engineering, on 25th September 2012
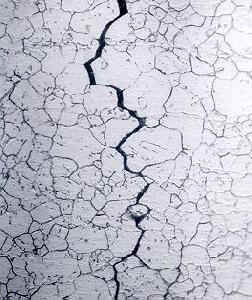
A little snippet of what I learned at university, residing deprecated in my skull, all of a sudden, during one the most boring of tests that we could think of for a component, became relevant and real. A part cracked during corrosion testing. Then another did, and another - and we had an issue, as they say in the modern parlance.
It was one of those things that, as soon as they occur, make you think “of course! Why didn’t we think of that before we started testing?” To which the answer is of course: because we didn’t know that we needed to think of it.
It was a lovely, clear case of stress corrosion cracking.
We were looking at making the switch from steel to aluminium for some joint components. We knew about some of the ways that Al differs from steel (no definable infinite fatigue life, galvanic potential in corrosive environments, for example) already. The test plan that we came up with was a fairly standard one that would more or less tick boxes so that we could introduce the product with a customer.
And then the stress corrosion cracking appeared. Fortunately, we had for various reasons chosen to test two different Al alloys - and sure enough, only one of them was affected by SCC. A quick Google search confirmed our findings: Al 7075 T6 is highly susceptible to SCC, whilst the 6xxx alloy that we also tried is not. You can read some of the literature we found here and here.
It turns out that the alloying elements (Zn, Mg and Cu) that make up 7075 T6 and its kin precipitate out to the grain boundaries during the T6 grade heat treatment. This inter-metallic phase forms an anode to the grains’ cathode, promoting corrosion along the grain boundaries (from a good discussion on Engineering Tips, here).
They also create inherent weaknesses in the overall structure. With a component under permanent stress (in our example we’re looking at around 10 kN clamping force), corrosion running between the grains uncovers a path for a crack to propagate.
Funnily enough, the crack wasn’t catastrophic, at least not in our nice, stable laboratory conditions: the joint was still tight. However, adding typical vehicle loads and system pressures to the joint would almost certainly lead to a reduced component life.
So - it’s clear: don’t use Al 7075 T6 in applications that can be exposed to corrosive environments whilst under load. The biggest question now is how to ensure that future Canny Engineers don’t fall into the same trap that this one did and end up with them feeling less canny than ever.
One part of the answer lies in the most obvious place of all, the drawing. But only part of the answer… We will of course remove Al 7075 T6 from the drawing and keep our Al 6xxx material on there. As this is a real product change, we will have to update the revision level on the print and obtain approval for that change. This means that we will enter our change request procedure, filling out the associated form. There, we will write a few lines about SCC, make reference to the test report - and that’s that. The change request document will be referenced on the drawing (remember to obtain the CR number before changing the drawing, then!), so the link is made. Anyone interested in the history of this part can, with a little digging, find the reason why we eliminated Al 7075 T6 from our prints.
Great - but that’s hardly a robust way of ensuring that future engineers will know to avoid it. They would have to chance upon the one print that was involved in our original “discovery” of SCC, when all other variants of this component would no longer have any reference to this change, because they would of course have been designed correctly from the outset… Until our future canny engineer says “hold on, why not use 7075 T6? It’s stronger, so we can use less of it… etc)” How do we as ghost of his past tell him that he’s in danger of no longer being canny?
This is where company Wikis, bodies of knowledge, collections of basic data, whatever you call it, need to be working well. Just relying on Google doesn’t work: I just put in “Al 7075 T6” into the search box and came up with 935000 results, and in the first several pages it all looks great - the perfect material for our application; which, of course, it was for us, until it wasn’t.
What I have started to do is to set up a technical Wiki for precisely such matters. It’s sparsely populated, and there are currently no other users - and the management don’t seem to have understood it - but it’s worth persevering with into 2013 so that my colleagues in 2031 don’t have to go through the stress of corrosion cracking.
Assuming that the system that runs my wiki is still extant…